On September 1st, 2016, SpaceX experienced a rather public setback when one of their Falcon 9 rockets exploded on its launchpad at the Cape Canaveral Launch Complex in Florida. Though the accident resulted in no fatalities or injuries, this accident has since raised concerns over at NASA concerning the company’s safety standards.
Such was the conclusion reached by NASA’s Space Station Advisory Committee, which met on Monday, Oct. 31st, to discuss the accident and make recommendations. In a statement, the committee indicated that SpaceX’s policy of fueling rockets immediately before launch could pose a serious threat to crewed missions.
These concerns have been expressed before, but have become all the more relevant in light of the recent accident. At the time of the explosion, the rocket was already outfitted with its cargo capsule (which contained the Spacecom Amos-6 communications satellite). In the future, SpaceX hopes to send crewed missions into space, which means crews’ lives could be at risk in the event that a similar accident takes place during fueling.
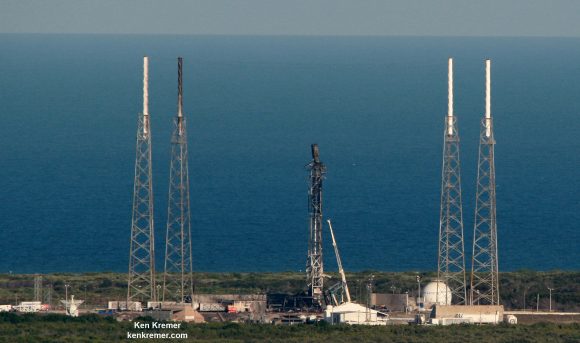
Lt. General Thomas Stafford (USAF), who chaired the committee, was especially emphatic about the need for SpaceX to review its fueling policy. According to The Wall Street Journal, this is the second time that Lt. Gen. Stafford has expressed concerns. The last time was in 2015, when he sent a letter to NASA arguing that the company’s policy of fueling a rocket with its cargo already on board went against decades of procedure.
In the past, NASA has always maintained a policy where a rocket’s cargo is added only after the rocket is fueled. The same goes for crewed missions, where astronauts would board the rocket or Shuttle only after all pre-flight procedures were finished. But in the age of NewSpace, and with private companies offering launch services, things work a little differently.
For example, SpaceX Falcon 9 rocket relies on a combination of liquid oxygen and rocket-grade kerosene propellant, which has less mass than conventional rocket fuel. This lets them pack more fuel into their rockets, and to be able to place larger payloads into orbit. However, this method requires that the rocket be immediately fueled before launch so that the fuel does not have time to warm up and expand.
As a result, future missions – which include crewed ones – will have to be fueled immediately before launch in order to ensure that the rocket’s fuel and lift capacity are not compromised. The Advisory Committee’s recommendations could therefore have a significant impact on how SpaceX does business. However, there recommendations might be a bit premature as far as crewed missions go.
For instance, the Dragon V2 has a crew abort system that was specifically designed for this kind of situation. Relying on the capsule’s eight side-mounted SuperDraco engines, this system is programmed to conduct a propulsive firing in the event of a catastrophic failure on the launchpad. The capsule also comes with a landing chute which will deploy once the rockets are depleted to ensure that it makes a soft landing.
In May of 2015, the company tested this system at the Cape Canaveral Launch Complex, followed by a “propulsive hovering test” in November of that same year. Both tests were successful and demonstrated how the SuperDraco engines are capable of launching the capsule to safety, and that they were capable of keeping the capsule in a state of equilibrium above the ground (see video above).
In addition, SpaceX responded to news of the Advisory Panel and expressed confidence in its procedures, which included fueling and their launch abort system. In an official statement, the full text of which was procured by Universe Today via email, the company said that:
“SpaceX has designed a reliable fueling and launch process that minimizes the duration and number of personnel exposed to the hazards of launching a rocket. As part of this process, the crew will safely board the Crew Dragon, ground personnel will depart, propellants will be carefully loaded over a short period, and then the vehicle will launch. During this time the Crew Dragon launch abort system will be enabled. Over the last year and a half, NASA and SpaceX have performed a detailed analysis of all potential hazards with this process.”
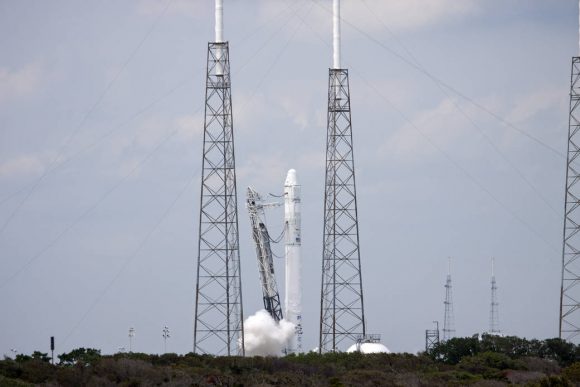
In addition, they cited that prior to the Sept.1st accident, all safety protocols had been followed and NASA had signed off on the launch. But of course, they also expressed that they would continue to comply with all safety procedures, which could include any changes based on the Advisory Committee’s recommendations:
“The hazard report documenting the controls was approved by the NASA’s Safety Technical Review Board in July 2016. As with all hazard analyses across the entire system and operations, controls against those hazards have been identified, and will be implemented and carefully verified prior to certification. There will be continued work ahead to show that all of these controls are in place for crewed operations and that the verifications meet NASA requirements. These analyses and controls will be carefully evaluated in light of all data and corrective actions resulting from the anomaly investigation. As needed, any additional controls will be put in place to ensure crew safety, from the moment the astronauts reach the pad, through fueling, launch, and spaceflight, and until they are brought safely home.”
In the meantime, SpaceX investigators are still attempting to find out exactly what went wrong with the Sept.1st launch. The most recent update (which was made on Oct. 28th) indicated that the company is making headway, and hoping to return to normal operations during the month of November.
“SpaceX’s efforts are now focused on two areas – finding the exact root cause, and developing improved helium loading conditions that allow SpaceX to reliably load Falcon 9,” it states. “With the advanced state of the investigation, we also plan to resume stage testing in Texas in the coming days, while continuing to focus on completion of the investigation.”
Further Reading: WSJ
I don’t know how I feel about this incident, and follow-up in general. Tom Stafford is legit, and I understand his concerns.
At the same time, Space X has been so phenomenally successful that I also wondered at what point the government would try to “rein the company in”, so to speak.
The explosion seems unique in that there is still no known explanation for it, even though Space X is trying to discover one. Space X employees were initially concerned about suspicious activity on a nearby roof at the launch complex, but it doesn’t sound like there has been a significant investigation into that.
Overall, it now sounds like the company is going to be more heavily regulated. And granted, it really could’ve been just an accident and could just be a reaction to that explosion, but it is also very convenient that this now affords the government an angle to regulate a private company that has been much more successful than NASA at reaching spaceflight goals over the past 5 years.
SpaceX is the best one.
I think the author is confusing fueling before launch with fueling before test firing. Virtually all rockets are fueled immediately prior to launch, within a few hours. Also, the cargo (except for humans) are always loaded onto the rocket after fueling. It would be extremely unsafe to hoist a satellite or space probe to the top of a fully-fueled launch vehicle.
Take the space shuttle for instance. The cargo was loaded in the verticle assembly building, the shuttle was rolled out to the pad, fueled a couple of hours before launch, the astronauts were added, and the stack was launched.
For uncrewed missions, such as a satellite launch on a Titan, the payload is added in the assembly building, the rocket rolled out to the pad, fueled on the pad, and launched.
However, for test firings, the payload is never in place under NASA procedures. For launches that include astronauts the spacecraft is already mounted before fueling but the astronauts are added just before launch, usually about two hours.
But NASA has never “maintained a policy where a rocket’s cargo is added only after the rocket is fueled.” This would be both impractical and very dangerous to try and hoist the payload on top of a fully-fueled rocket on the pad.
I urge Mr. Williams to clarify and revise this article for the sake of accuracy.
WROOONG!
on Shuttle, the payload was loaded on pad using the rotating service structure.
As I understand it, the rotating service structure is designed for loading the Shuttle. Not for attaching payloads to the top of a rocket.
Here is a picture of the unit used for attaching rocket upper stage payload.
http://www.nasa.gov/sites/default/files/images/588318main_2011-08-02-2-1600_226-170.jpg
Umm… sorry FROSTY, RickRusty is correct.
No confusion. The SpaceX explosion took place during a test firing, at which time, the cargo was already loaded. And as was said in the article, SpaceX procedures are to fuel at the last minute so that their liquid oxygen fuel won’t warm up and expand. It is this very practice with the NASA Advisory Committee is concerned about and for which they met. I’m afraid it is you who is in the wrong here.
Some military payloads are loaded onto Atlas V rockets on the pad but they are encapsulated in the fairing and the rocket is for sure unfueled. There is no way NASA ever loaded an unencapsulated payload in open air into the shuttle, this was always done inside the VAB. The rotary structure you’re talking about is a service structure for the stack.
Once and rocket begins to be fueled almost every one, if not every one at all, is cleared from the area. It would be extremely dangerous to try and bolt a payload weighing thousands of pounds on a rocket containing tons of highly volatile fuels. To my knowledge it has never been done.
The article is seriously flawed and should be corrected or pulled.
“For example, SpaceX Falcon 9 rocket relies on a combination of liquid oxygen and rocket-grade kerosene propellant, which has less mass than conventional rocket fuel.”
This is so wrong that it makes it clear that the author truly does not understand what is going on, and probably shouldn’t be writing more on topics like this until he’s done some serious reading on the topic so as not to misinform readers.
1) The F9 uses RP-1. This is a (very) standard issue rocket propellant. SpaceX does nothing unusual with their RP-1. It isn’t densified, it isn’t spike with anything. It’s the same crap everyone else uses.
2) RP-1 is actually a high mass rocket fuel. Hydrogen would be a low mass rocket fuel. SpaceX does not use hydrogen.
3) What SpaceX *does* do differently is use sub-chilled LOX (liquid oxygen), unlike basically everyone else. Most rockets use LOX that is right at its boiling point, but SpaceX uses LOX that is near its freezing point. The density of LOX is highly temperature dependent, so sub-chilling it to near freezing allows a significantly greater mass of LOX to be loaded into the same volume of fuel tank.
I’m not sure how the author got those three things so wrong in their mind in the quoted statement, but there you go. Below is the rest of what happened:
_______________________
4) SpaceX uses composite helium tanks, which almost no one else does. Most use titanium helium bottles, which are much heavier.
5) SpaceX puts its helium tanks in the LOX tanks, which almost no one else does (the LOX keeps the helium colder than it would otherwise be, allowing (once again) more helium to fit into a small, low mass tank).
6) The combination of those three things – sub-chilled LOX, composite helium bottles, and helium bottles inside the LOX tank – has never been done before. However, it allows significantly more payload to be taken to orbit by lowering the mass of the second stage’s structure. Every gram of additional structure that you put on the second stage dramatically decreases your ultimate payload to orbit.
7) Because no one has ever done this before, no one had ever seen this particular failure modality. In this case near-freezing LOX was induced to freeze onto the composite helium bottles. This eventually weakened the composite structure of one of the bottles, allowing the high pressure helium inside to rupture the bottle.
8) #7 was probably caused by the particular way (temperature, pressure) that helium was loaded into the bottles on this particular fueling test.
It seems there is no shortage of people attempting to find fault here, and being incredibly petty in the process. Nitpicking a minor detail does not make the statements “so wrong”.
These aren’t minor details.
As an example, it’s as if you were a sports reporter covering a baseball game, and kept talking about how the score was “15-Love”, and about how the “actors” were trying to cricket the puck through the uprights. Sure those words sound “sportsie”, but anyone with even a cursory understanding of baseball would have their jaw on the floor, wondering how anyone could write such an incomprehensible article.
Just to be clear: I rarely find reason criticize UT articles (they’re usually pretty good, with better than average background information and accuracy). I’m also not calling you stupid;). That said, you wrote an article with huge amounts of misinformation in it. You also don’t even seem to realize what you did, due to a fundamental lack of knowledge about the subject you’re writing on.
My suggestion: keep reading everything you can on these subjects. And keep writing articles. We’ll keep criticizing you. Eventually you’ll have read enough that everything you write will be fantastic, and we will have no cause to complain:)!
Umm.. Rusty. RP-1 IS highly refined kerosene. Matt is NOT wrong. Ahem…Google RP-1 friend and you will see.. perhaps?
You’re replying to me, and yes, I know what RP-1 is. The author said that RP-1 “isn’t conventional rocket fuel”. Yes, yes it is. It is *the* conventional rocket fuel.
No, I said that SpaceX doesn’t use conventional rocket fuel in that they don’t use it alone. I said they use it and ac combination of LOX. Between that and nitpicking how they keep LOX colder than others, you’re criticisms are entirely superficial and more than a little petty.
From what I’ve heard… the problem’s root cause is that frozen Helium is much colder than LOX. The He tank is located inside the LOX tank. The temp. difference between the two cryogenic liquids apparently burst the composite He tank as the He expanded from a liquid state to gas. That abrupt pressure change ruptured the He tank. That led to the LOX tank overpressuring then exploding. The fix may be to fuel-up more slowly? Or more insulation for the He tank?
Although the language may have been petty, I’m afraid that Rick and Gopher have it right. It’s not a matter of semantics. It’s useful information vs. the lack of critical context.
Based on the original post and the author’s replies to the comments, my impressions are as follows:
1) SpaceX uses a different grade of kerosene, where others use heavier fuels;
2) others usually don’t use helium;
and that’s about it.
It seems arbitrary, and then Musk’s tweets didn’t make much sense, saying that a ruptured helium tank caused the explosion. That just doesn’t make sense because helium isn’t flammable. So, I thought, well, maybe some shrapnel from the ruptured helium tank struck the LOX tank or kerosene tank?
After reading through the comment section, then the whole thing makes much more sense. SpaceX basically uses the same kerosene, LOX and helium that everyone else uses for the same reasons.
The critical differences are that SpaceX puts the helium tank INSIDE the LOX tank. Now, Musk’s tweet makes sense! And the lighter composite material of the helium tank is a new twist to the industry, posing unknowns related to longevity and reliability, combined with cooling the fuels to substantially lower levels than common industry practices to maximize the amount of fuel on board.
The reasons for doing all of this are illuminating, including the efficiency advantages of cooling the LOX and keeping the cooled helium tank in the LOX tank. It seems very efficient on multiple levels, from minimizing the energy needed to cool everything, putting the helium where it is going to be used (maintaining pressure in the LOX tank), and leveraging lighter materials.
So, we now see what they actually do differently, why they do it that way, and therefore where the risks are.
I like all of the articles on Universe Today, including of this author. Apparently, this article got away.