One of the most exciting things about space exploration today is the ways in which it is getting more cost-effective. Between reusable rockets, miniaturized electronics, and low-cost launch services, space is becoming more accessible and populated. However, this also presents a challenge when it comes to conventional methods for maintaining spacecraft and satellites.
One of the biggest challenges is packing electronics into tighter spaces, which makes it harder to keep them at operational temperatures. To address this, engineers at NASA are developing a new system known as microgap-cooling technology. During two recent test flights, NASA demonstrated that this method is effective at removing heat and can also function in a weightless environment.
These test flights were funded through NASA’s Flight Opportunities program, which is a part of the Space Technology Mission Directorate with additional support provided by the agency’s Center Innovation Fund. The tests were conducted using a Blue Origin’s New Shepard rocket, which transported the system to suborbital altitudes and then returned it to Earth.

The entire time, the system’s functionality was monitored from NASA’s Goddard Space Flight Center by NASA engineer Franklin Robinson and Avram Bar-Cohen (an engineer from the University of Maryland). What they found was that the microgap-cooling system was able to able to remove large amounts of heat from tightly-packed integrated circuits.
What’s more, the system worked in both low- and high-gravity environments with nearly identical results. As Robinson explained:
“Gravity effects are a big risk in this type of cooling technology. Our flights proved that our technology works under all conditions. We think this system represents a new thermal-management paradigm.”
With this new technology, the heat generated by tightly-packed electronics is removed by a non-conducting fluid (known as HFE 7100) that flows through microchannels embedded within or between the circuits and produces vapor. This process allows for a higher rate of heat transfer which can ensure that high-powered electronic devices will be less likely to fail due to overheating.
This represents a big departure from conventional cooling approaches, where electronic circuits are arranged out in a two-dimensional layout that keeps heat-generating hardware elements far away from each other. Meanwhile, the heat generated by electrical circuits is transferred to the circuit board and eventually directed towards a spacecraft-mounted radiator.
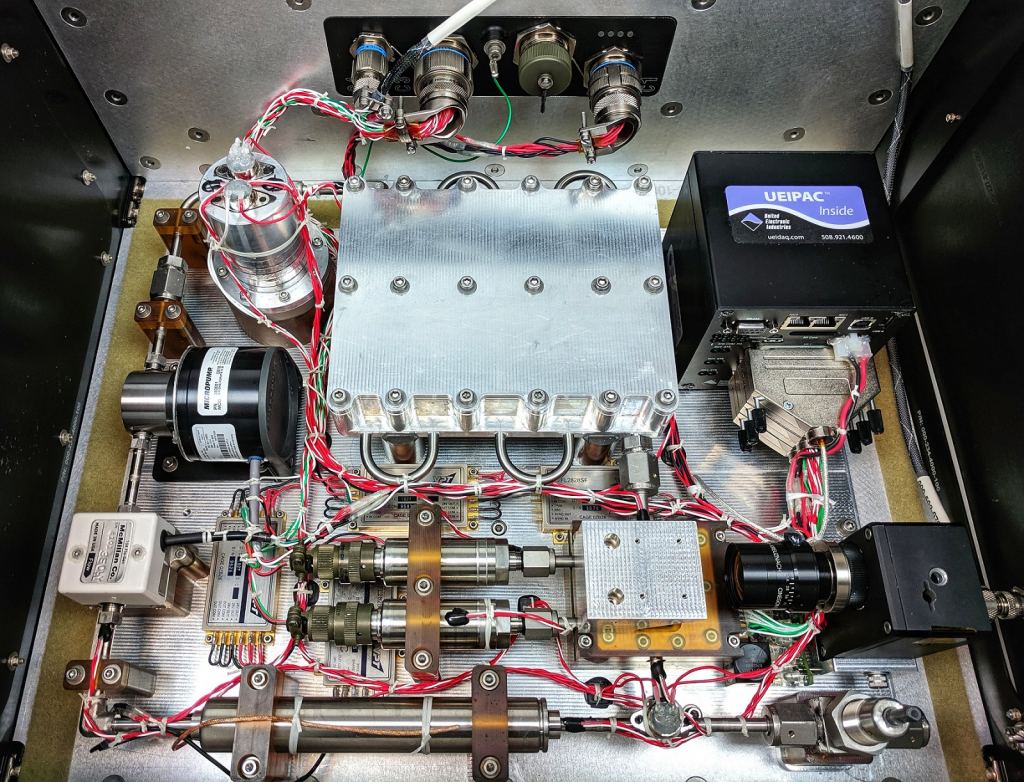
This technology takes advantage of 3D circuitry, an emerging technology where circuits are literally stacked one on top of another with interconnecting wiring. This allows for shorter distances between chips and superior performance since data can be transferred both vertically and horizontally. It also allows for electronics that consume less energy while also taking up less space.
Roughly four years ago, Robinson and Bar-Cohen began investigating this technology for the purposes of spaceflight. Integrated into satellites and spacecraft, 3D circuits would be able to accommodate power-dense electronics and laser heads, which are also decreasing in size and need better systems for removing waste heat.
Previously, Robinson and Bar-Cohen had successfully tested the system in a laboratory environment. These flight tests, however, demonstrated that it works in space and under varying gravity environments. For this reason, Robinson and Bar-Cohen believe the technology may be ready for integration into actual missions.
Further Reading: NASA