We may be living in the Golden Age of Mars Exploration. With multiple orbiters around Mars and two functioning rovers on the surface of the red planet, our knowledge of Mars is growing at an unprecedented rate. But it hasn’t always been this way. Getting a lander to Mars and safely onto the surface is a difficult challenge, and many landers sent to Mars have failed.
The joint ESA/Roscosmos Mars Express mission, and its Chiaparelli lander, is due at Mars in only 15 days. Now’s a good time to look at the challenges in getting a lander to Mars, and also to look back at the many failed attempts.
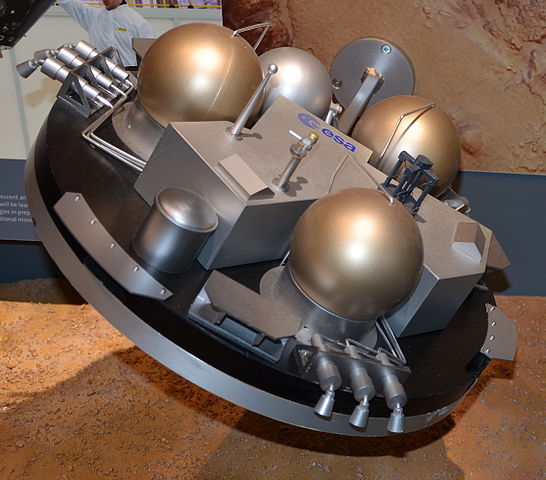
For now, NASA has the bragging rights as the only organization to successfully land probes on Mars. And they’ve done it several times. But they weren’t the first ones to try. The Soviet Union tried first.
The USSR sent several probes to Mars starting back in the 1960s. They made their first attempt in 1962, but that mission failed to launch. That failure illustrates the first challenge in getting a craft to land on Mars: rocketry. We’re a lot better at rocketry than we were back in the 1960’s, but mishaps still happen.
Then in 1971, the Soviets sent a pair of probes to Mars called Mars 2 and Mars 3. They were both orbiters with detachable landers destined for the Martian surface. The fate of Mars 2 and Mars 3 provides other illustrative examples of the challenges in getting to Mars.
Mars 2 separated from its orbiter successfully, but crashed into the surface and was destroyed. The crash was likely caused by its angle of descent, which was too steep. This interrupted the descent sequence, which meant the parachute failed to deploy. So Mars 2 has the dubious distinction of being the first man-made object to reach Mars.
Mars 3 was exactly the same as Mars 2. The Soviets liked to do missions in pairs back then, for redundancy. Mars 3 separated from its orbiter and headed for the Martian surface, and through a combination of aerodynamic breaking, rockets, and parachutes, it became the first craft to make a soft landing on Mars. So it was a success, sort of.
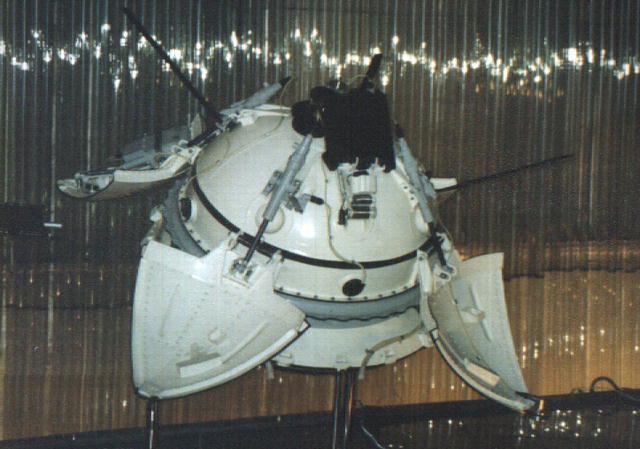
But after only 14.5 seconds of data transmission, it went quiet and was never heard from again. The cause was likely an intense dust storm. In an odd turn of events, NASA’s Mariner 9 orbiter reached Mars only days before Mars 2 and 3, becoming the first spacecraft to orbit another planet. It captured images of the planet-concealing dust storms, above which only the volcanic Olympus Mons could be seen. These images provided an explanation for the failure of Mars 3.
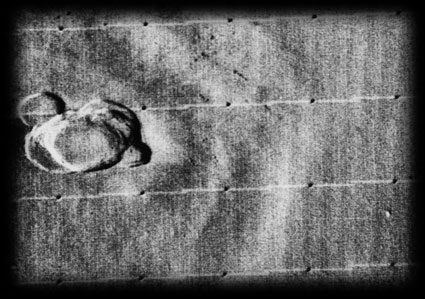
In 1973, the Soviets tried again. They sent four craft to Mars, two of which were landers, named Mars 6 and Mars 7. Mars 6 failed on impact, but Mars 7’s fate was perhaps a little more tragic. It missed Mars completely, by about 1300 km, and is in a helicentric orbit to this day. In our day and age, we just assume that our spacecraft will go where we want them to, but Mars 7 shows us that it can all go wrong. After all, Mars is a moving target.
In the 1970s, NASA was fresh off the success of their Apollo Program, and were setting their sites on Mars. They developed the Viking program which saw 2 landers, Viking 1 and Viking 2, sent to Mars. Both of them were probe/lander configurations, and both landers landed successfully on the surface of Mars. The Vikings sent back beautiful pictures of Mars that caused excitement around the world.
![The Viking 2 lander captured this image of itself on the Martian surface. By NASA - NASA website; description,[1] high resolution image.[2], Public Domain, https://commons.wikimedia.org/w/index.php?curid=17624](https://www.universetoday.com/wp-content/uploads/2016/10/608px-Viking2lander1.jpg)
In 1997, NASA’s Martian Pathfinder made it to Mars and landed successfully. Pathfinder itself was stationary, but it brought a little rover called Sojourner with it. Sojourner explored the immediate landing area around Pathfinder. Sojourner became the first rover to operate on another planet.
Pathfinder was able to send back over 16,000 images of Mars, along with its scientific data. It was also a proof of concept mission for technologies such as automated obstacle avoidance and airbag mediated touchdown. Pathfinder helped lay the groundwork for the Mars Exploration Rover Mission. That means Spirit and Opportunity.
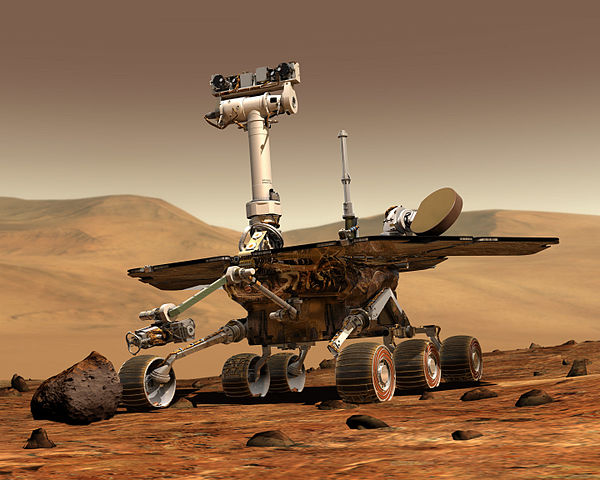
But after Pathfinder, and before Spirit and Opportunity, came a time of failure for Martian landing attempts. Everybody took part in the failure, it seems, with Russia, Japan, the USA, and the European Space Agency all experiencing bitter failure. Rocket failures, engineering errors, and other terminal errors all contributed to the failure.
Japan’s Nozomi orbiter ran out of fuel before ever reaching Mars. NASA’s Mars Polar Lander failed its landing attempt. NASA’s Deep Space 2, part of the Polar Lander mission, failed its parachute-less landing and was never heard from. The ESA’s Beagle 2 lander made it to the surface, but two of its solar panels failed to deploy, ending its mission. Russian joined in the failure again, with its Phobos-Grunt mission, which was actually headed for the Martian moon Phobos, to retrieve a sample and send it back to Earth.
In one infamous failure, engineers mixed up the use of English units with Metric units, causing NASA’s Mars Climate Orbiter to burn up on entry. These failures show us that failure is not rare. It’s difficult and challenging to get to the surface of Mars.
After this period of failure, NASA’s Spirit and Opportunity rovers were both unprecedented successes. They landed on the Martian surface in January 2004. Both exceeded their planned mission length of three months, and Opportunity is still going strong now.
So where does that leave us now? NASA is the only one to have successfully landed a rover on Mars and have the rover complete its mission. But the ESA and Russia are determined to get there.
The Schiaparelli lander, as part of the ExoMars mission, is primarily a proof of technology mission. In fact, its full name is the Schiaparelli EDM lander, meaning Entry, Descent, and Landing Demonstrator Module.
It will have some small science capacity, but is really designed to demonstrate the ability to enter the Martian atmosphere, descend safely, and finally, to land on the surface. In fact, it has no solar panels or other power source, and will only carry enough battery power to survive for 2-8 days.
Schiaparelli faces the same challenges as other craft destined for Mars. Once launched successfully, which it was, it had to navigate its way to Mars. That took about 6 months, and since ExoMars is only 15 days away from arrival at Mars, it looks like it has successfully made its way their. But perhaps the trickiest part comes next: atmospheric entry.
Schiaparelli is like most Martian craft. It will make a ballistic entry into the Martian atmosphere, and this has to be done right. There is no room for error. The angle of entry is the key here. If the angle is too steep, Schiaparelli may overheat and burn up on entry. On the other hand, if the angle is too shallow, it could hit the atmosphere and bounce right back into space. There’ll be no second chance.
The entry and descent sequence is all pre-programmed. It will either work or it won’t. It would take way too long to send any commands to Schiaparelli when it is entering and descending to Mars.
If the entry is successful, the landing comes next. The exact landing location is imprecise, because of wind speed, turbulence, and other factors. Like other craft sent to Mars, Schiaparelli’s landing site is defined as an ellipse.
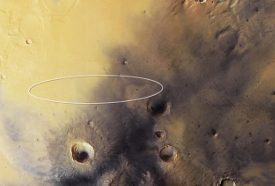
The lander will be travelling at over 21,000 km/h when it reaches Mars, and will have only 6 or 7 minutes to descend. At that speed, Schiaparelli will have to withstand extreme heating for 2 or 3 minutes. It’s heat shield will protect it, and will reach temperatures of several thousand degrees Celsius.
It will decelerate rapidly, and at about 10km altitude, it will have slowed to approximately 1700 km/h. At that point, a parachute will deploy, which will further slow the craft. After the parachute slows its descent, the heat shield will be jettisoned.
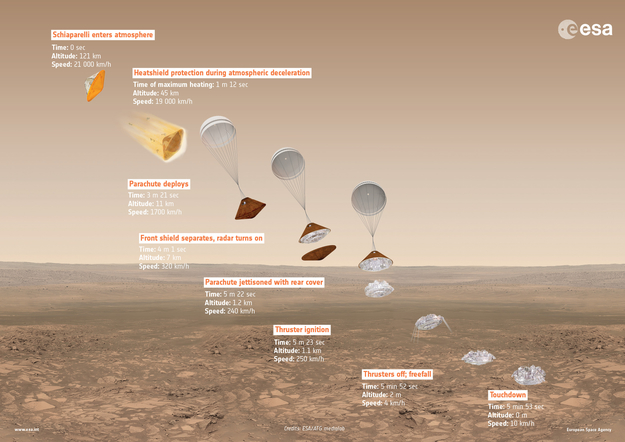
On Earth, a parachute would be enough to slow a descending craft. But with Mars’ less dense atmosphere, rockets are needed for the final descent. An onboard radar will monitor Schiaparelli’s altitude as it approaches the surface, and rockets will fire to slow it to a few meters per second in preparation for landing.
In the final moments, the rockets will stop firing, and a short free-fall will signal Schiaparelli’s arrival on Mars. If all goes according to plan, of course.
We won’t have much longer to wait. Soon we’ll know if the ESA and Russia will join NASA as the only agencies to successfully land a craft on Mars. Or, if they’ll add to the long list of failed attempts.