
KENNEDY SPACE CENTER VISITOR COMPLEX, FL – Following up last week’s announcement of NASA’s proposed Fiscal Year 2018 top line budget of $19.1 Billion by the Trump Administration, Universe Today spoke to NASA’ s Kennedy Space Center (KSC) Director Robert Cabana to get his perspective on the new budget and what it means for NASA and KSC; “Stay on the path!” – with SLS, Orion, ISS and Commercial Crew was his message in a nutshell.
The highlights of NASA’s $19.1 Billion FY 2018 budget request were outlined last week by NASA Acting Administrator Robert Lightfoot during a ‘State of NASA’ speech to agency employees held at NASA HQ, Washington, D.C. and broadcast to the public live on NASA TV on May 23.
In order to get a better idea of the implications of the 2018 NASA budget proposal for KSC, I spoke one-on-one with Robert Cabana – one of NASA’s top officials, who currently serves as Director of the Kennedy Space Center (KSC) as well as being a former astronaut and Space Shuttle Commander. Cabana is a veteran of four space shuttle missions.
How did NASA and KSC fare with the newly announced 2018 Budget?
“We at KSC and NASA as a whole did very well with the 2018 budget,” KSC Director Robert Cabana explained during an interview with Universe Today by the Rocket Garden at the Kennedy Space Center Visitor Complex (KSCVC) in Florida.
“I think it really solidifies that the President has confidence in us, on the path that we are on,” Cabana noted while attending a student robotics competition at KSCVC sponsored by NASA.
“With only a 1 percent cut – when you look at what other agency’s got cut – this budget allows us to stay on the path that we are on.”
Trump cut NASA’s 2018 budget request by $0.5 Billion compared to the recently enacted FY 2017 budget of $19.6 Billion approved by the US Congress and signed by the President.
Other Federal science agency’s also critically vital to the health of US scientific research such as the NIH, the NSF, the EPA, DOE and NIST suffered terrible double digit slashes of 10 to 20% or more.
KSC is the focal point for NASA’s human spaceflight programs currently under intense development by NASA – namely the Space Launch System (SLS) Mars megarocket, the Orion deep space crew capsule to be launched beyond Earth orbit (BEO) atop SLS, and the duo of Commercial Crew Program (CCP) space taxis being manufactured by Boeing and SpaceX that will ferry our astronauts to low Earth orbit (LEO) and the International Space Station (ISS).
Numerous NASA science missions also launch from the Florida Space Coast.
“At KSC the budget keeps us on a path that continues to provide a commercial crew vehicle to fly crews to the ISS in 2018,” Cabana stated.
“The budget also keeps us on track to launch SLS and Orion in 2019.”
“I think that’s really important – along with all the other stuff we are doing here at KSC.”
“From our point of view it’s a good budget. We need to press ahead and continue on with what we promised.”
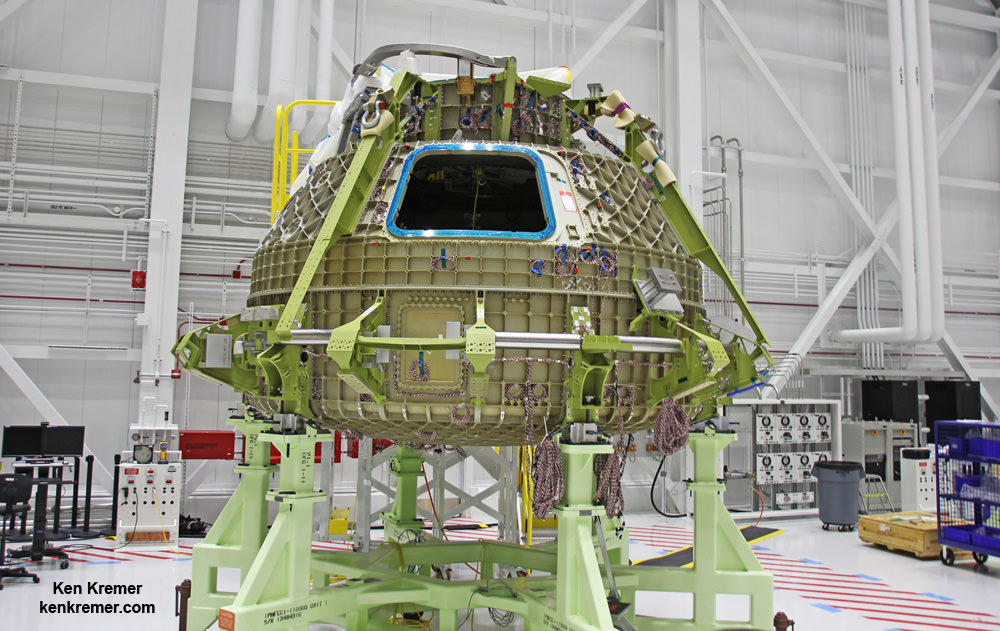
What’s ahead for commercial crew at KSC?
“We are moving forward with commercial crew,” Cabana told me.
“Within the next calendar year [2018] we are moving ahead with flying the first certification flight with crew to the ISS. So that’s test flights and by the end of the year an actual crewed flight to the ISS. I want to see that happen.”

Industry partners Boeing and SpaceX are building the private CST-100 Starliner and Crew Dragon spaceships respectively, as part of NASA’s commercial crew initiative aimed at restoring America’s human spaceflight capability to launch our astronauts aboard American spaceships on American rockets from American soil.
Commercial Crew is a public/private partnership initiative with commercial contracts valued at $4.2 Billion and signed by Boeing and SpaceX with NASA in September 2014 under the Obama Administration.
The goal of commercial crew is to end our sole reliance on the Russian Soyuz capsule for astronaut flights to the space station since the retirement of the space shuttles back in 2011 – by manufacturing indigenous rockets and human rated spaceships.
However the CCP program suffered severe budget reductions by the US Congress for several years which forced significant work stretch-outs and delays in the maiden crew launches by both companies from 2015 to 2018 – and thus forced additional payments to the Russians for Soyuz seat purchases.
Both the Boeing Starliner and SpaceX Dragon crew vehicles can carry 4 or more astronauts to the ISS. This will enable NASA to add another crew member and thereby enlarge the ISS crew from 6 to 7 permanent residents after they become operational.
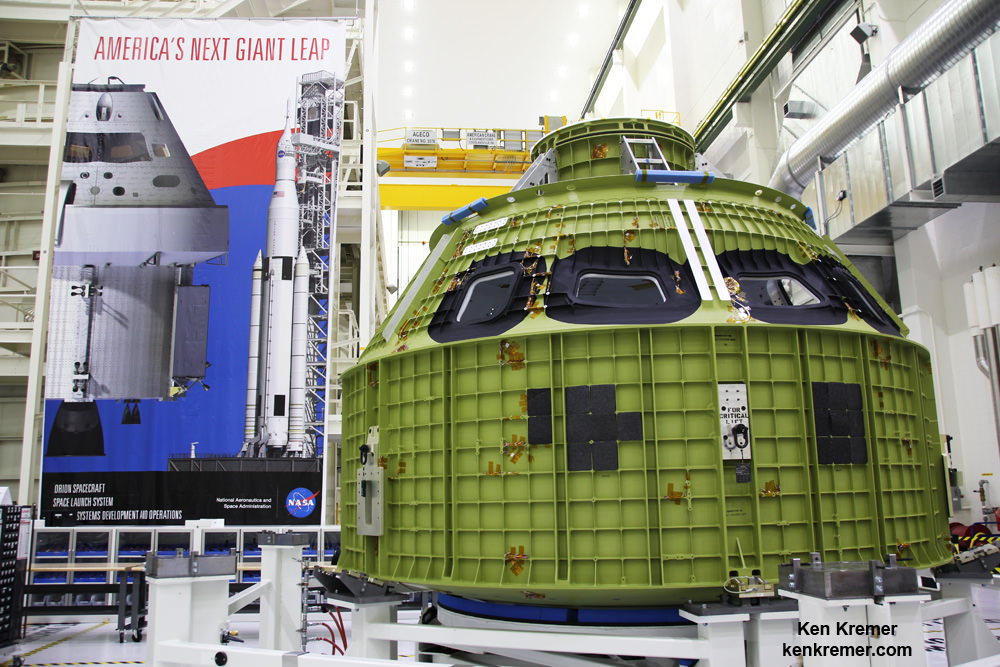
Meanwhile NASA is focusing on developing the SLS heavy lift rocket and Orion crew capsule with prime contractors Boeing and Lockheed Martin in an agency wide effort to send humans on a ‘Journey to Mars’ in the 2030s.
The European Space Agency(ESA) is also partnered with NASA and providing the service module for Orion.
What’s the status of the delivery of the European Space Agency’s service module?
“The service module will be here sometime next year,” Cabana said.
He noted that the details and exact timing are yet to be determined.
The first integrated launch of SLS and Orion on the unpiloted Exploration Mission-1 (EM-1) is now slated for sometime in 2019 after NASA recently slipped the date to the right from Fall 2018.
At the request of the Trump Administration, NASA also just completed a detailed study to ascertain the feasibility of adding a crew of two NASA astronauts to the EM-1 flight and launch it by the end of 2019.
In the end, NASA officials decided to stick with the baselined plan of no crew on EM-1 for a variety of technical and safety reasons, as well as cost – as I reported here.
I asked Cabana for his insight and opinion on NASA not adding crew to Orion on the EM-1 flight.
“No we are not launching crew on the first flight [EM-1],” Cabana stated.
“With the budget that we have and what we need to do, this is the answer we got to at the end.”
“You know the crew study was still very important. It allowed us to find some things that we should still do on [EM-1], even though we are not going to launch crew on that flight.
“So we will make some further modifications that will reduce the risk even further when we do fly crew [on the next flight of EM-2].”
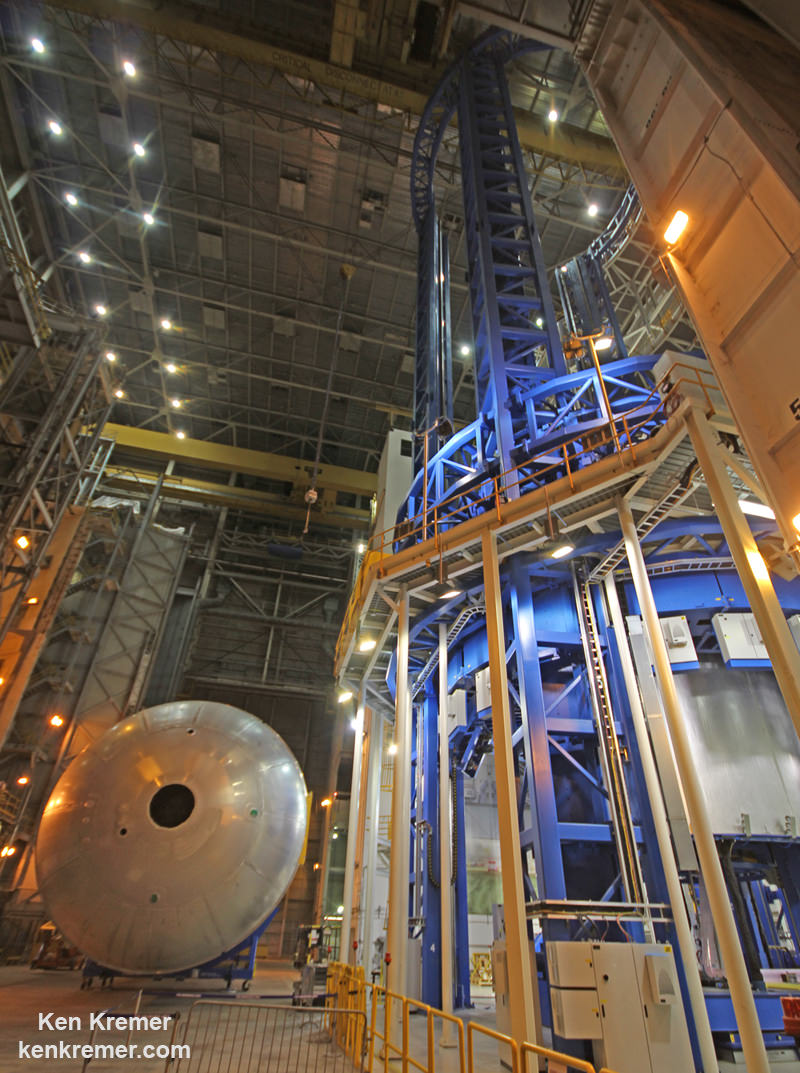
So for 2017 what are the major milestone you hope to complete here at KSC for SLS and Orion?
“So for me here at the Kennedy Space Center, my goal for the end of this calendar year 2017 we will have completed all of the construction of all of the [ground systems] hardware and facilities that are necessary to process and launch the Space Launch System (SLS) and Orion,” Cabana elaborated.
‘We will still have a lot of work to do with the software for the spacecraft command and control systems and the ground systems.”
“But my goal is to have the hardware for the ground systems complete by the end of this year.”
What are those KSC facilities?
“Those facilities include the VAB [Vehicle Assembly Building] which will be complete to accept the mobile launcher in September and pad 39B will be complete in August,” Cabana said.
“The RPSF is already complete. The NPFF is already complete and we are doing testing in there. The LASF [Launch Abort System Facility] is complete – where they put the abort rocket on.”
“The Mobile Launcher will be complete from a structural point of view, with all the systems installed by the end of the year [including the umbilical’s and while room].”

Watch for Ken’s onsite CRS-11 mission reports direct from the Kennedy Space Center and Cape Canaveral Air Force Station, Florida.
Stay tuned here for Ken’s continuing Earth and Planetary science and human spaceflight news.
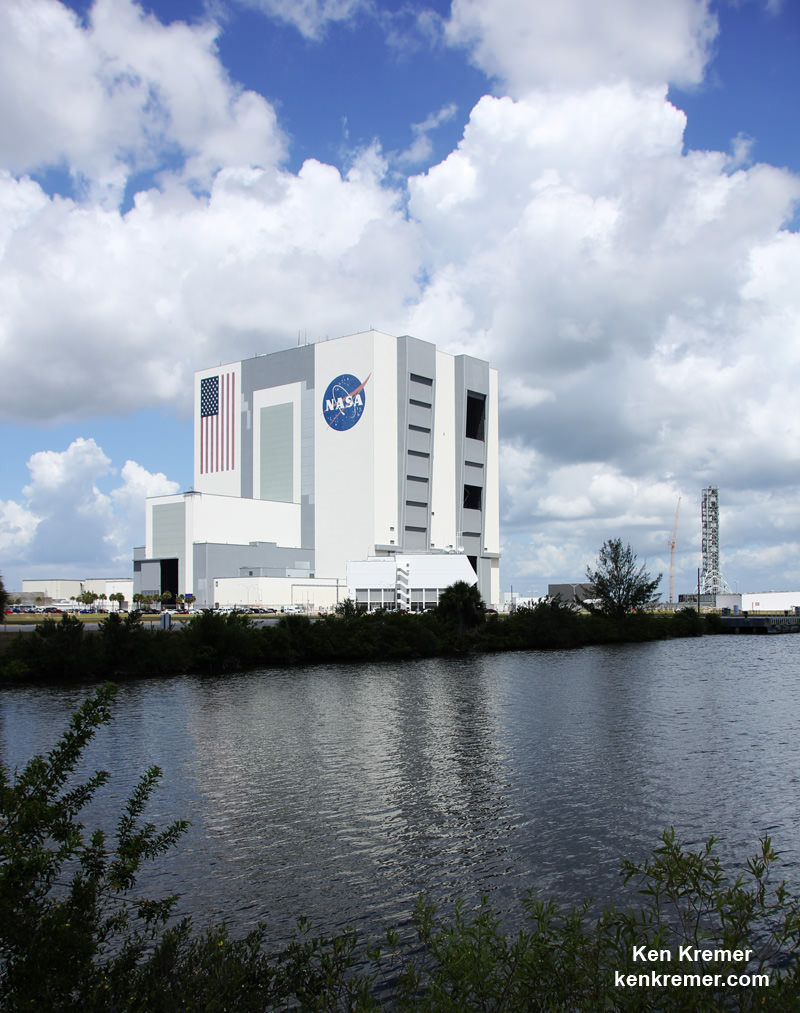
.……….
Learn more about the SpaceX Dragon CRS-11 resupply launch to ISS, NASA missions and more at Ken’s upcoming outreach events at Kennedy Space Center Quality Inn, Titusville, FL:
May 30/31: “SpaceX CRS-11 and CRS-10 resupply launches to the ISS, Inmarsat 5 and NRO Spysat, EchoStar 23, SLS, Orion, Commercial crew capsules from Boeing and SpaceX , Heroes and Legends at KSCVC, ULA Atlas/John Glenn Cygnus launch to ISS, SBIRS GEO 3 launch, GOES-R weather satellite launch, OSIRIS-Rex, Juno at Jupiter, InSight Mars lander, SpaceX and Orbital ATK cargo missions to the ISS, ULA Delta 4 Heavy spy satellite, Curiosity explores Mars, Pluto and more,” Kennedy Space Center Quality Inn, Titusville, FL, evenings
