Astronauts aboard the International Space Station have manufactured their first tool using the 3D printer on board the station. This is another step in the ongoing process of testing and using additive manufacturing in space. The ability to build tools and replacement parts at the station is something NASA has been pursuing keenly.
The first tool printed was a simple wrench. This may not sound like ground-breaking stuff, unless you’ve ever been in the middle of a project only to find you’re missing a simple tool. A missing tool can stop any project in its tracks, and change everybody’s plans.
The benefits of manufacturing needed items in space are obvious. Up until now, every single item needed on the ISS had to be sent up via re-supply ship. That’s not a quick turnaround. Now, if a tool is lost or destroyed during normal use, a replacement can be quickly manufactured on-site.
This isn’t the first item to be printed at the station. The first one was printed back in November 2014. That item was a replacement part for the printer itself. This was important because it showed that the machine can be used to keep itself running. This reliability is key if astronauts are going to be able to rely on the printer for manufacturing critical replacements for components and spare parts.
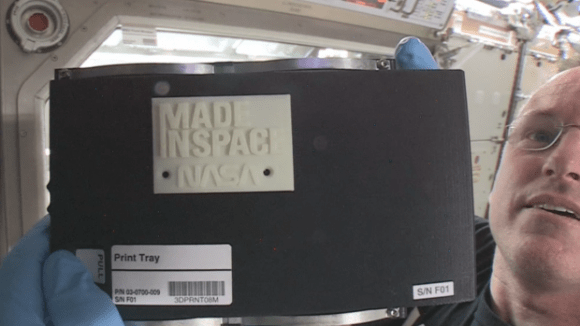
Niki Werkheiser, the project manager for the ISS 3D printer, said in a NASA YouTube video, “Since the inception of the human space program, we have been completely dependent on launching every single thing we need from Earth to space … I think we’re making history for the first time ever being able to make what we need when we need it in space.”
The 3D printer, which is more accurately called an Additive Manufacturing Facility (AMF) was built by a company called Made In Space. The one that was used to make the first tool is actually a different one than was used to make the replacement part for the printer itself. The first one was part of a test in 2014 to see how 3D printing would work in microgravity. It printed several items which were returned to Earth for testing. Those tests went well, which led to the second one being sent to the station.
This second machine, which was used to create the wrench, is a much more fully featured, commercial 3D printer. According to Made In Space, this newer AMF “can be accessed by any Earth-bound customer for job-specific work, like a machine shop in space. Example use cases include a medical device company prototyping space-optimized designs, or a satellite manufacturer testing new deployable geometries, or creating tools for ISS crew members.”
This is exciting news for we space enthusiasts, but even more exciting for a certain engineering student from the University of Alabama. The student, Robert Hillan, submitted a tool design to a NASA competition called the Future Engineers Space Tool design competition. The challenge was to design a tool that could be used successfully by astronauts in space. The catch was that the tool design had to upload to the ISS electronically and be printed by the AMF on the station.
In January, Hillan was announced as the winner. His design? The Multipurpose Precision Maintenance Tool, a kind of multi-tool that handy people are familiar with. The tool allows astronauts to tighten and loosen different sizes of nuts and bolts, and to strip wires.
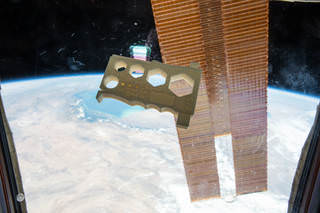
NASA astronaut Tim Kopra, who is currently aboard the ISS, praised both Hillan and the 3D printing technology itself. “When you have a problem, it will drive specific requirements and solutions. 3-D printing allows you to do a quick design to meet those requirements. That’s the beauty of this tool and this technology. You can produce something you hadn’t anticipated and do it on short notice.”
The immediate and practical benefits of AMF in space are obvious and concrete. But like a lot of space technologies, it is part of a larger picture, too.
Werkheiser, NASA’s project manager for the ISS 3D printer, said “If a printer is critical for explorers, it must be capable of replicating its own parts, so that it can keep working during longer journeys to places like Mars or an asteroid. Ultimately, one day, a printer may even be able to print another printer.”
So there we have it. A journey to Mars and printers replicating themselves. Bring it on.