Yes, she’s a little worse for wear, isn’t she? But then again, that’s what atmospheric re-entry and 2200 °Celsius (4000 °Fahrenheit) worth of heat will do to you! Such was the state of the heat shield that protected NASA’s Orion Spaceship after it re-entered the atmosphere on Dec. 5th, 2014. Having successfully protected the craft during it’s test flight, the shield was removed and transported to the Marshall Space Flight Center in Huntsville, Alabama, where it arrived on March. 9th.
Since that time, a steady stream of NASA employees have been coming by the facility to get a look at it while engineers collect data and work to repair it. In addition to being part of a mission that took human-rated equipment farther out into space than anything since the Apollo missions, the heat shield is also living proof that NASA is restoring indigenous space capability to the US.
First unveiled by NASA in May of 2011, the Orion Multi-Purpose Crew Vehicle (MPCV) was intrinsic to the Obama administration’s plan to send astronauts to a nearby asteroid by 2025 and going to Mars by the mid-2030’s. In addition to facilitating these long-range missions, the Orion spacecraft would also handle some of the routine tasks of spaceflight, such as providing a means of delivering and retrieving crew and supplies from the ISS.
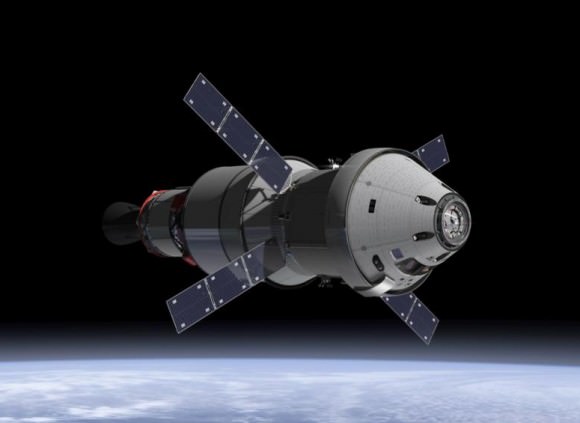
The uncrewed test flight that took place on December 5, 2014, known as Exploration Flight Test 1 (EFT-1), was intended to test various Orion systems, including separation events, avionics, heat shielding, parachutes, and recovery operations prior to its debut launch aboard the Space Launch System,
This design of this mission corresponded to the Apollo 4 mission of 1967, which demonstrated the effectiveness of the Apollo flight control systems and the heat shields ability to withstand re-entry conditions, as part of the spacecraft’s return from lunar missions.
After being retrieved, the heat shield was transported by land to the Marshall Space Flight Center, where it was offloaded and transferred to a large support structure so engineers could perform studies on it for the next three months.
This will consist of collecting samples from the shield to measure their char layers and degree of erosion and ablation, as well as extracting the various instruments embedded in the heat shield to assess their performance during re-entry.
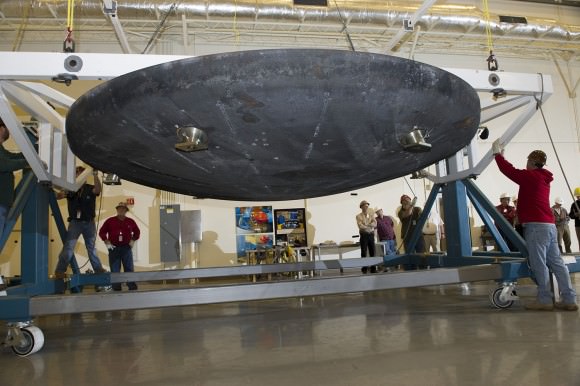
After the analysis is complete, technicians will load the shield into the 7-axis milling machine and machining center, where it will be grind down to remove the remaining material covering. Known as Avcoat, this heat-retardant substance is similar to what the Apollo missions used, with the exception of toxic materials like asbestos.
This material is used to fill the 320,000 honeycomb-like cells that make up the outer layer of the shield. When heated, the material burns away (aka. ablates) in order to prevent heat being transferred into the crew module. This shield is placed over the craft’s titanium skeleton and carbon-fiber skin, providing both protection and insulation for the interior.
Once all the Avcoat is removed and only the skeletal frame remains, it will be shipped to the Langley Research Center in Hampton, Virginia, for more tests. Since the Orion was returning from a greater distance in space than anything since Apollo, it experienced far greater heat levels than anything in recent decades, reaching as high as 2200 °C (4000 °F).
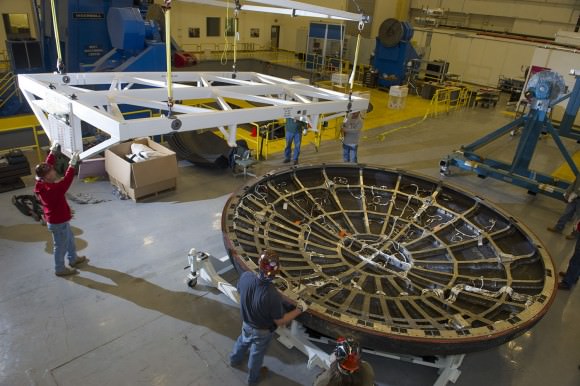
Instrumentation in the shield measured the rise of the surface and internal temperatures during re-entry as well as the ablation rate of the shield’s coating. Over the next few months, NASA experts will be pouring over this data to see just how well the Orion shield held up under extreme heat. But so far, the results look positive – with only 20% of the Avcoat burning away on the test-flight re-entry.
In the future, the Orion spacecraft will be launched on Space Launch System on missions that will take it to nearby asteroids and eventually Mars. The first mission to carry astronauts is not expected to take place until 2021 at the earliest.
Further Reading: NASA