By the time a rocket actually launches, it’s components have been through a ton of rigorous testing. That’s certainly true of NASA’s SLS (Space Launch System) which is the most powerful rocket ever built. That’s right, something is finally going to surpass the Saturn V, the rocket that took Apollo astronauts to the Moon.
Continue reading “Watch NASA Test an SLS Tank to Destruction”Japan’s First Private Rocket Flies to Space
Have you heard of Interstellar Technologies? They’re the latest private company to launch their own rocket into space. They’re a Japanese company, and like other private space companies, their stated goal is to lower the cost to access space.
Continue reading “Japan’s First Private Rocket Flies to Space”This is How NASA Releases Almost Half a Million Gallons of Water in 60 Seconds
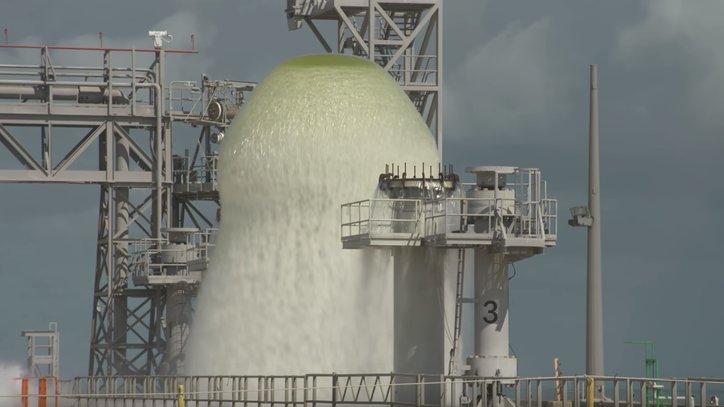
As rockets become more and more powerful, the systems that protect them need to keep pace. NASA will use almost half a million gallons of water to keep the Space Launch System (SLS) safe and stable enough to launch successfully. The system that delivers all that water is called the Ignition Overpressure Protection and Sound Suppression (IOP/SS) water deluge system, and seeing it in action is very impressive.
Continue reading “This is How NASA Releases Almost Half a Million Gallons of Water in 60 Seconds”
Engineers Propose a Rocket that Consumes Itself as it Flies to Space
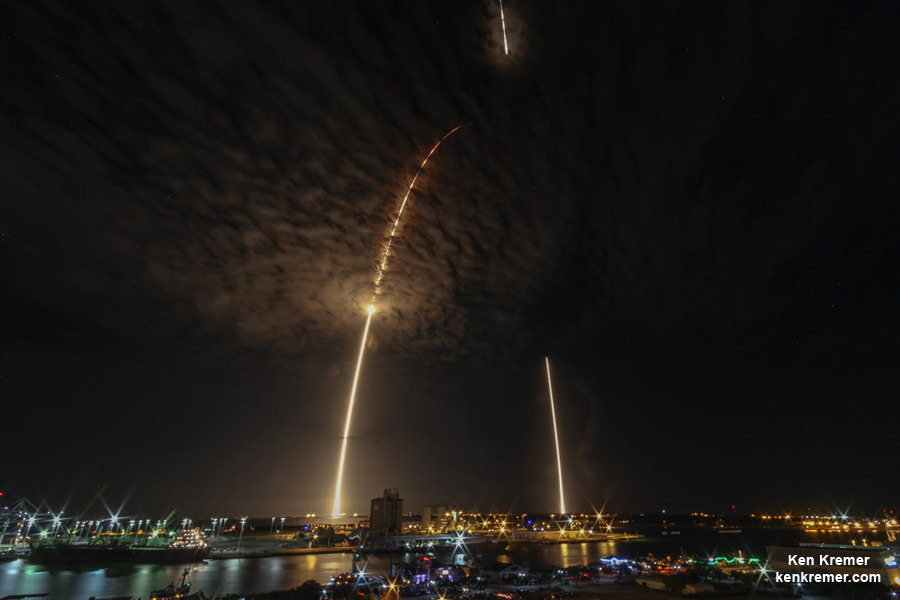
When it comes to the new era of space exploration, one of the primary focuses has been on cutting costs. By reducing the costs associated with individual launches, space agencies and private aerospace companies will not only be able to commercialize Low Earth-Orbit (LEO), but also mount far more in the way of exploration missions and maybe even colonize space.
Several methods have been proposed so far for reducing launch costs, which include reusable rockets and single-stage-to-orbit rockets. However, a team of engineers from the University of Glasgow and the Ukraine recently proposed an entirely different idea that could make launching small payloads affordable – a self-eating rocket! This “autophage” rocket could easily send small satellites into space more easily and more affordably.
The study which describes how they built and tested the “autophage” engine recently appeared in the Journal of Spacecraft and Rockets under the title “Autophage Engines: Toward a Throttleable Solid Motor“. The team was led by Vitaly Yemets and Patrick Harkness – a Professor from the Oles Honchar Dnipro National University in the Ukraine and a Senior Lecturer from the University of Glasgow, respectively.
Together, the team addressed one the most pressing issues when it comes to rockets today. This has to do with the fact that storage tanks, which contain the rocket’s propellants as they climb, weight many times the spacecraft’s payload. This reduces the efficiency of the launch vehicle and also adds to the problem of space debris, since these fuel tanks are disposable and fall away when spent.
As Dr Patrick Harkness, who led Glasgow’s contribution to the work, explained in a recent University of Glasgow press release:
“Over the last decade, Glasgow has become a centre of excellence for the UK space industry, particularly in small satellites known as ‘CubeSats’, which provide researchers with affordable access to space-based experiments. There’s also potential for the UK’s planned spaceport to be based in Scotland. However, launch vehicles tend to be large because you need a large amount of propellant to reach space. If you try to scale down, the volume of propellant falls more quickly than the mass of the structure, so there is a limit to how small you can go. You will be left with a vehicle that is smaller but, proportionately, too heavy to reach an orbital speed.”
In contrast, an autophage engine consumes its own structure during ascent, so more cargo capacity could be freed-up and less debris would enter orbit. The propellant consists of a solid fuel rod (made of a solid plastic like polyethylene) on the outside and an oxidizer on the inside. By driving the rod into a hot engine, the fuel and oxidizer are vaporized to create gas that then flows into the combustion chamber to produce thrust.
“A rocket powered by an autophage engine would be different,” said Dr. Harkness. “The propellant rod itself would make up the body of the rocket, and as the vehicle climbed the engine would work its way up, consuming the body from base to tip. That would mean that the rocket structure would actually be consumed as fuel, so we wouldn’t face the same problems of excessive structural mass. We could size the launch vehicles to match our small satellites, and offer more rapid and more targeted access to space.”
The research team also showed that the engine could be throttled by simply varying the speed at which the rod is driven into the engine, which is something rare in a solid motor. During the lab tests, the team has been able to sustain rocket operations for 60 seconds at a time. As Dr. Harkness said, the team hopes to build on this and eventually conduct a launch test:
“While we’re still at an early stage of development, we have an effective engine testbed in the laboratory in Dnipro, and we are working with our colleagues there to improve it still further. The next step is to secure further funding to investigate how the engine could be incorporated into a launch vehicle.”
Another challenge of the modern space age is how to deliver additional payloads and satellites into orbit without creating more in the way of orbital clutter. By introducing an engine that can make for cheap launches that also has no disposable parts, the autophage could be a game-changing technology, one which is right up there with fully-recoverable rockets.
The research team also consisted of Mykola Dron and Anatoly Pashkov – a Professor and Senior Researcher from Oles Honchar Dnipro National University – and Kevin Worrall and Michael Middleton – a Research Associate and M.S. student from the University of Glasgow.
Further Reading: University of Glasgow, Journal of Spacecraft and Rockets
Launching Rockets from Balloons is About to be a Thing, But We Need a Better Name than “Rockoons”
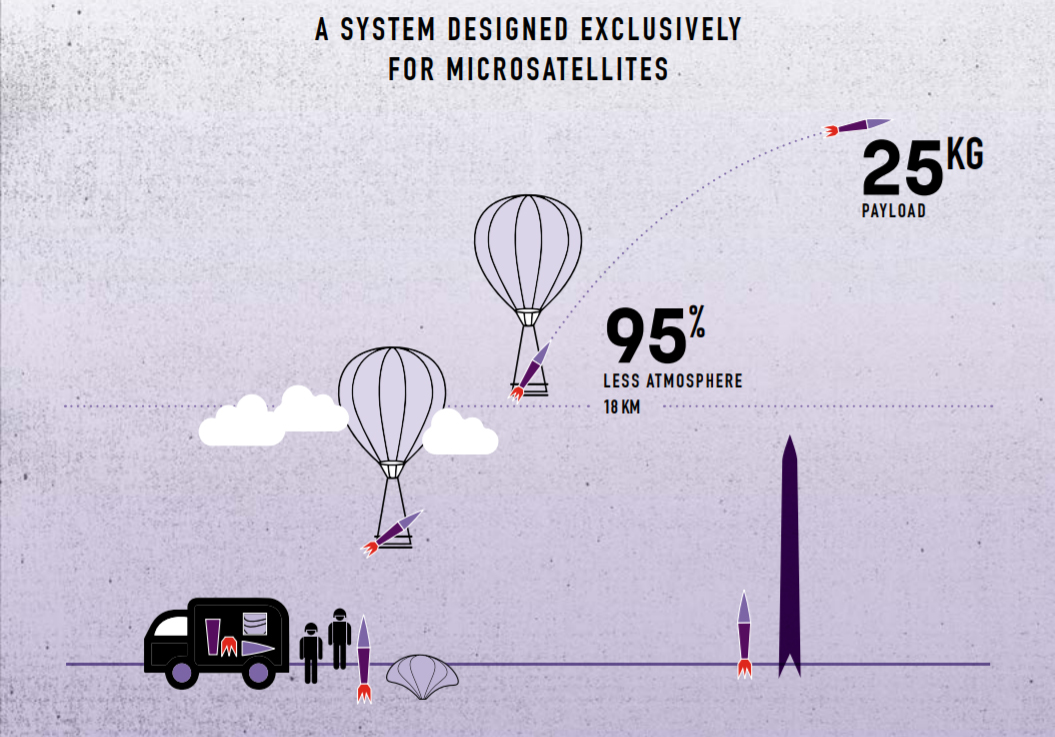
One of the technological hurdles of our age is to get people and equipment into space more cheaply. SpaceX gets a lot of the headlines around that, with their reusable rockets. And so does Blue Origin, to some degree. Now a small start-up affiliated with Purdue University is tackling the problem and making some headway.
The company is called Leo Aerospace LLC and they’re using balloons to lower the cost of putting micro-satellites into orbit, rather than reusable rockets. The balloons will be reusable, but the rockets won’t.
Leo Aerospace plans to revive a decades-old method of putting satellites into space. They’re using hot air balloons to lift the rocket and its micro-satellite payload 18 km (11 miles) above Earth. At that altitude, there’s 95% less atmosphere. This means much less drag on the rocket, which translates into smaller rockets with less fuel. This is an intriguing idea, if not for the unfortunate name.
The rockoons will be used to launch rockets into sub-orbital and orbital flights. Sub-orbitals are often used by researchers because it gives them access to zero gravity and to vacuum, both of which are necessary for some experiments. According to Leo Aerospace, there’s something revolutionary about their plans.
“We’re targeting the microsatellites by saying, ‘You don’t have to ride-share with anyone. We can guarantee you will be our only payload and we will be focused on you.’” – Drew Sherman, Leo Aerospace’s Head of Vehicle Development.
They intend on targeting micro-satellite developers. Micro-satellites are often hitch-hikers on larger payloads, which basically means they’re second-class customers. They have to wait until there’s room for their micro-satellite on a traditional rocket carrying a larger payload. This can mean long delays of several months, and that micro-satellite developers have to compromise when it comes to the orbits they can obtain. It can also make micro-satellite missions difficult to plan and execute efficiently and economically. Micro-satellites are becoming more and more capable, so having a launch system tailor-made for them could indeed be revolutionary.
“We’re targeting the microsatellites by saying, ‘You don’t have to ride-share with anyone. We can guarantee you will be our only payload and we will be focused on you,’” said Drew Sherman, Leo Aerospace’s head of vehicle development. “‘We will work with you exclusively to get you into orbit. You won’t have to worry about other payloads or getting dropped off in the wrong spot.’”
The flexibility of the rockoon system that Leo Aerospace is developing will be intriguing for micro-satellites. Rockoons will give micro-satellites the flexibility they need to operate efficiently. The launch can be scheduled and adapted to the needs of the individual satellite. “Our goal is to give people access to space. The only way to do that right now is to help people get their satellite into orbit. That’s where we want to leave our mark,” said Abishek Murali, Head of Mission Engineering at Leo Aerospace.
“Our goal is to give people access to space.” – Abishek Murali, Head of Mission Engineering at Leo Aerospace
The rockoon itself is a hybrid of a balloon and a rocket. The hybrid design takes advantage of physics by using the balloon to float the rocket 18 km high before launching the rocket. The rockoon has Leo Aerospace’s own patent-pending technology to control the pitch and angle of the launch, allowing for precision launches.
Rockoons were first used by the US Air Force back in the 1950s. But this next generation of rockoons, coupled with modern micro-satellites, will be much more capable than the 1950s technology.
Currently, Leo Aerospace is in the development and funding phase. They’ve obtained some funding from the National Science Foundation, and from a venture capital firm. They have about half of the $250,000 they need. They plan to conduct their first sub-orbital flight in 2020, and to launch their first micro-satellite into orbit in 2022. They intend to use existing approved launch sites.
Leo Aerospace was founded by five then-students at Purdue University. Leo started as a club, but the former students have turned it into a business. And that business seems to have a bright future. They conducted a customer discovery and market validation study and found a large demand for a better way to launch micro-satellites.
“We want to be part of the space market,” Murali said. “People are interested in space and creating technologies that not only can operate in space but also help people back on Earth. What we’re trying to do is help them get there.”
But they still need a better name than “rockoons.”
Astronomy Cast Ep. 483: Stopping in Space
It’s one thing to get from Earth to space, but sometimes you want to do the opposite. You want to get into orbit or touch down gently on the surface of a planet and explore it. How do spacecraft stop? And what does that even mean when everything is orbiting?
We usually record Astronomy Cast every Friday at 3:00 pm EST / 12:00 pm PST / 20:00 PM UTC. You can watch us live on AstronomyCast.com, or the AstronomyCast YouTube page.
Visit the Astronomy Cast Page to subscribe to the audio podcast!
If you would like to support Astronomy Cast, please visit our page at Patreon here – https://www.patreon.com/astronomycast. We greatly appreciate your support!
If you would like to join the Weekly Space Hangout Crew, visit their site here and sign up. They’re a great team who can help you join our online discussions!
Astronomy Cast Ep. 479: Rockets pt. 1 – What Does “Single Stage To Orbit” Really Mean?
To celebrate the launch of the Falcon Heavy, we figured it was time for an all new series, this time on the rockets that carry us to space. Today we’re going to talk about why single stage to orbit rockets are so difficult to carry out.
We usually record Astronomy Cast every Friday at 3:00 pm EST / 12:00 pm PST / 20:00 PM UTC. You can watch us live on AstronomyCast.com, or the AstronomyCast YouTube page.
Visit the Astronomy Cast Page to subscribe to the audio podcast!
If you would like to support Astronomy Cast, please visit our page at Patreon here – https://www.patreon.com/astronomycast. We greatly appreciate your support!
If you would like to join the Weekly Space Hangout Crew, visit their site here and sign up. They’re a great team who can help you join our online discussions!
Canada To Get Its Own Spaceport
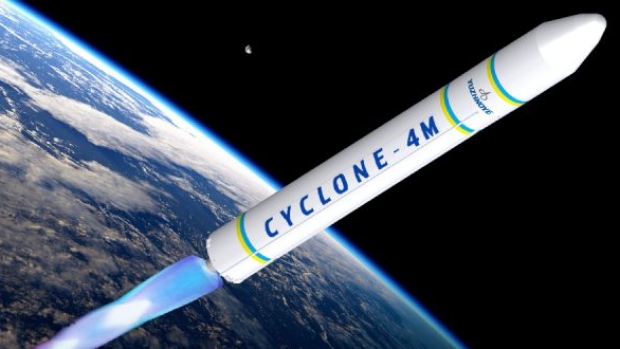
Canada is getting its own rocket-launching facility. Maritime Launch Services (MLS) has confirmed its plans to build and operate a commercial launch facility in Nova Scotia, on Canada’s east coast. The new spaceport should begin construction in 1 year, and should be in operation by 2022.
The facility will be built near Canso, in the province of Nova Scotia. Maritime Launch Services hopes to launch 8 rockets per year to place satellites in orbit. The Ukrainian Cyclone 4M medium-class rockets that will lift-off from Canso will have a payload of up to 3,350 kg.
The red marker in the map above shows the location of the Maritime Launch Services spaceport. Image: Google
Spaceports have certain requirements that make some locations more desirable. They need to be near transportation infrastructure so that rockets, payloads, and other materials can be transported to the site. They need to be away from major population centres in case of accidents. And they need to provide trajectories that give them access to desirable orbits.
The Nova Scotia site isn’t the only location considered by MLS. They evaluated 14 sites in North America before settling on the Canso, NS site, including ones in Mexico and the US. But it appears that interest and support from local governments helped MLS settle on Canso.
The Ukrainian Cyclone M4 rockets have an excellent track record for safety. The company who builds it, Yuzhnoye, has been in operation for 62 years and has launched 875 vehicles and built and launched over 400 spacecraft. Cyclone rockets have launched successfully 221 times.
MLS is a group of American aerospace experts including people who have worked with NASA. They are working with the makers of the Cyclone 4 rocket, who have wanted to open up operations in North America for some time.
The Cyclone rocket family first started operating in 1969. The Cyclone 4 is the newest and most powerful rocket in the Cyclone family. It’s a 3-stage rocket that runs on UDMH fuel and uses nitrogen tetroxide for an oxidizer.
There have been other proposals for a Canadian spaceport. The Canadian Space Agency was interested in Cape Breton, also in Nova Scotia, as a launch site for small satellites in 2010. A Canadian-American consortium called PlanetSpace also looked at a Nova Scotia site for a launch facility, but they failed to get the necessary funding from NASA in 2008. Fort Churchill, in the Province of Manitoba, was the site of over 3,500 sub-orbital flights before being shut down in 1985.
The Canso launch facility is an entirely private business proposal. Neither the Canadian government nor the Canadian Space Agency are partners. It’s not clear if having a launch facility on Canadian soil will impact the CSA’s activities in any way.
But at least Canadians won’t have to leave home to watch rocket launches.
Falcon Heavy Vs. Saturn V
Its an Epic Rocket Battle! Or a Clash of the Titans, if you will. Except that in this case, the titans are the two of the heaviest rockets the world has ever seen. And the contenders couldn’t be better matched. On one side, we have the heaviest rocket to come out of the US during the Space Race, and the one that delivered the Apollo astronauts to the Moon. On the other, we have the heaviest rocket created by the NewSpace industry, and which promises to deliver astronauts to Mars.
And in many respects, the Falcon Heavy is considered to be the successor of the Saturn V. Ever since the latter was retired in 1973, the United States has effectively been without a super-heavy lifter. And with the Space Launch System still in development, the Falcon Heavy is likely to become the workhorse of both private space corporations and space agencies in the coming years.
So let’s compare these two rockets, taking into account their capabilities, specifications, and the history of their development and see who comes out on top. BEGIN!
Development History:
The development of the Saturn V began in 1946 with Operation Paperclip, a US government program which led to the recruitment of Wernher von Braun and several other World War II-era German rocket scientists and technicians. The purpose of this program was to leverage the expertise of these scientists to give the US an edge in the Cold War through the development of intercontinental ballistic missiles (ICBMs).
Between 1945 and the mid-to-late 50s von Braun acted as an advisor to US armed forces for the sake of developing military rockets only. It was not until 1957, with the Soviet launch of Sputnik-1 using an R-7 rocket – a Soviet ICBM also capable of delivering thermonuclear warheads – that the US government began to consider the use of rockets for space exploration.
Thereafter, von Braun and his team began developing the Jupiter series of rockets – a modified Redstone ballistic missile with two solid-propellant upper stages. These proved to be a major step towards the Saturn V, hence why the Jupiter series was later nicknamed “an infant Saturn”. Between 1960 and 1962, the Marshall Space Flight Center began designing the rockets that would eventually be used by the Apollo Program.
After several iterations, the Saturn C-5 design (later named the Saturn V) was created. By 1964, it was selected for NASA’s Apollo Program as the rocket that would conduct a Lunar Orbit Rendezvous (LRO). This plan called for a large rocket to launch a single spacecraft to the Moon, but only a small part of that spacecraft (the Lunar Module) would actually land on the surface. That smaller module would then rendezvous with the main spacecraft – the Command/Service Module (CSM) – in lunar orbit and the crew would return home.
Development of the Falcon Heavy was first announced in 2011 at the National Press Club in Washington D.C. In a statement, Musk drew direct comparisons to the Saturn V, claiming that the Falcon Heavy would deliver “more payload to orbit or escape velocity than any vehicle in history, apart from the Saturn V moon rocket, which was decommissioned after the Apollo program.”
Consistent with this promise of a “super heavy-lift” vehicle, SpaceX’s original specifications indicated a projected payload of 53,000 kg (117,000 lbs) to Low-Earth Orbit (LEO), and 12,000 kgg (26,000 lbs) to Geosynchronous Transfer Orbit (GTO). In 2013, these estimates were revised to 54,400 kg (119,900 lb) to LEO and 22,200 kg (48,900 lb) to GTO, as well as 16,000 kilograms (35,000 lb) to translunar trajectory, and 13,600 kilograms (31,000 lb) on a trans-Martian orbit to Mars, and 2,900 kg (6,400 lb) to Pluto.
In 2015, the design was changed – alongside changes to the Falcon 9 v.1.1 – to take advantage of the new Merlin 1D engine and changes to the propellant tanks. The original timetable, proposed in 2011, put the rocket’s arrival at SpaceX’s west-coast launch location – Vandenberg Air Force Base in California – at before the end of 2012.
The first launch from Vandenberg was take place in 2013, while the first launch from Cape Canaveral was to take place in late 2013 or 2014. But by mid-2015, delays caused by failures with Falcon 9 test flights caused the first launch to be pushed to late 2016. The rocket has also been relocated to the Kennedy Space Center Launch Complex in Florida.
SpaceX also announced in July 0f 2016 that it planned to expand its landing facility near Cape Canaveral to take advantage of the reusable technology. With three landing pads now planned (instead of one on land and a drone barge at sea), they hope to be able to recover all of the spent boosters that will be used for the launch of a Falcon Heavy.
Design:
Both the Saturn V and Falcon Heavy were created to do some serious heavy lifting. Little wonder, since both were created for the sole purpose of “slipping the surly bonds” of Earth and putting human beings and cargo onto other celestial bodies. For its part, the Saturn V‘s size and payload surpassed all other previous rockets, reflecting its purpose of sending astronauts to the Moon.
With the Apollo spacecraft on top, it stood 111 meters (363 feet) tall and was 10 meters (33 feet) in diameter, without fins. Fully fueled, the Saturn V weighed 2,950 metric tons (6.5 million pounds), and had a payload capacity estimated at 118,000 kg (261,000 lbs) to LEO, but was designed for the purpose of sending 41,000 kg (90,000 lbs) to Trans Lunar Insertion (TLI).
Later upgrades on the final three missions boosted that capacity to 140,000 kg (310,000 lbs) to LEO and 48,600 kg (107,100 lbs) to the Moon. The Saturn V was principally designed by NASA’s Marshall Space Flight Center in Huntsville, Alabama, while numerous subsystems were developed by subcontractors. This included the engines, which were designed by Rocketdyne, a Los Angeles-based rocket company.
The first stage (aka. S-IC) measured 42 m (138 feet) tall and 10 m (33 feet) in diameter, and had a dry weight of 131 metric tons (289,000 lbs) and a total weight of over 2300 metric tons (5.1 million lbs) when fully fueled. It was powered by five Rocketdyne F-1 engines arrayed in a quincunx (four units arranged in a square, and the fifth in the center) which provided it with 34,000 kN (7.6 million pounds-force) of thrust.
The Saturn V consisted of three stages – the S-IC first stage, S-II second stage and the S-IVB third stage – and the instrument unit. The first stage used Rocket Propellant-1 (RP-1), a form of kerosene similar to jet fuel, while the second and third stages relied on liquid hydrogen for fuel. The second and third stage also used solid-propellant rockets to separate during launch.
The Falcon Heavy is based around a core that is a single Falcon 9 with two additional Falcon 9 first stages acting as boosters. While similar in concept to the Delta IV Heavy launcher and proposals for the Atlas V HLV and Russian Angara A5V, the Falcon Heavy was specifically designed to exceed all current designs in terms of operational flexibility and payload. As with other SpaceX rockets, it was also designed to incorporate reusability.
The rocket relies on two stages, with the possibility of more to come, that measure 70 m (229.6 ft) in height and 12.2 m (39.9 ft) in width. The first stage is powered by three Falcon 9 cores, each of which is equipped with nine Merlin 1D engines. These are arranged in a circular fashion with eight around the outside and one in th middle (what SpaceX refers to as the Octaweb) in order to streamline the manufacturing process. Each core also includes four extensible landing legs and grid fins to control descent and conduct landings.
The first stage of the Falcon Heavy relies on Subcooled LOX (liquid oxygen) and chilled RP-1 fuel; while the upper stage also uses them, but under normal conditions. The Falcon Heavy has a total sea-level thrust at liftoff of 22,819 kN (5,130,000 lbf) which rises to 24,681 kN (5,549,000 lbf) as the craft climbs out of the atmosphere. The upper stage is powered by a single Merlin 1D engine which has a thrust of 34 kN (210,000 lbf) and has been modified for use in a vacuum.
Although not a part of the initial Falcon Heavy design, SpaceX has been extending its work with reusable rocket systems to ensure that the boosters and core stage can be recovered. Currently, no work has been announced on making the upper stages recoverable as well, but recent successes recovering the first stages of the Falcon 9 may indicate a possible change down the road.
The consequence of adding reusable technology will mean that the Falcon Heavy will have a reduced payload to GTO. However, it will also mean that it will be able to fly at a much lower cost per launch. With full reusability on all three booster cores, the GTO payload will be approximately 7,000 kg (15,000 lb). If only the two outside cores are reusable while the center is expendable, the GTO payload would be approximately 14,000 kg (31,000 lb).
Cost:
The Saturn V rocket was by no means a small investment. In fact, one of the main reasons for the cancellation of the last three Apollo flights was the sheer cost of producing the rockets and financing the launches. Between 1964 and 1973, a grand total of $6.417 billion USD was appropriated for the sake of research, development, and flights.
Adjusted to 2016 dollars, that works out to $41.4 billion USD. In terms of individual launches, the Saturn V would cost between $185 and $189 million USD, of which $110 million was spent on production alone. Adjusted for inflation, this works out to approximately $1.23 billion per launch, of which $710 million went towards production.
By contrast, when Musk appeared before the US Senate Committee on Commerce, Science and Transportation in May 2004, he stated that his ultimate goal with the development of SpaceX was to bring the total cost per launch down to $1,100 per kg ($500/pound). As of April 2016, SpaceX has indicated that a Falcon Heavy could lift 2268 kg (8000 lbs) to GTO for a cost of $90 million a launch – which works out to $3968.25 per kg ($1125 per pound).
No estimates are available yet on how a fully-reusable Falcon Heavy will further reduce the cost of individual launches. And again, it will vary depending on whether or not the boosters and the core, or just the external boosters are recoverable. Making the upper stage recoverable as well will lead to a further drop in costs, but will also likely impact performance.
Specifications:
So having covered their backgrounds, designs and overall cost, let’s move on to a side-by-side comparison of these two bad boys. Let’s see how they stack up, pound for pound, when all things are considered – including height, weight, lift payload, and thrust.
Saturn V: | Falcon Heavy: | |
Height: | 110.6 m (363 ft) | 70 m (230 ft) |
Diameter: | 10.1 m (33 ft) | 12.2 m (40 ft) |
Weight: | 2,970,000 kg (6,540,000 lbs) |
1,420,788 kg (3,132,301 lb) |
Stages: | 3 | 2+ |
Engines (1st Stage): |
5 Rocketdyne F-1 | 3 x 9 Merlin 1D |
2nd stage | 5 Rocketdyne J-2 | 1 Merlin 1D |
3rd stage | 1 Rocketdyne J-2 | |
Thrust (1st stage): |
34,020 kN |
22,918 kN (sea level); |
2nd stage | 4,400 kN | 934 kN |
3rd stage | 1,000 kN | |
Payload (LEO): | 140,000 kg (310,000 lbs) |
54,400 kg (119,900 lbs) |
Payload (TLI): | 48,600 kg (107,100 lbs) |
16,000 kg |
When put next to each other, you can see that the Saturn V has the advantage when it comes to muscle. It’s bigger, heavier, and can deliver a bigger payload to space. On the other hand, the Falcon Heavy is smaller, lighter, and a lot cheaper. Whereas the Saturn V can put a heavier payload into orbit, or send it on to another celestial body, the Falcon Heavy could perform several missions for every one mounted by its competitor.
But whereas the contributions of the venerable Saturn V cannot be denied, the Falcon Heavy has yet to demonstrate its true worth to space exploration. In many ways, its like comparing a retired champion to an up-and-comer who, despite showing lots of promise and getting all the headlines, has yet to win a single bout.
But should the Falcon Heavy prove successful, it will likely be recognized as the natural successor to the Saturn V. Ever since the latter was retired in 1973, NASA has been without a rocket with which to mount long-range crewed missions. And while heavy-lift options have been available – such as the Delta IV Heavy and Atlas V – none have had the performance, payload capacity, or the affordability that the new era of space exploration needs.
In truth, this battle will take several years to unfold. Only after the Falcon Heavy is rigorously tested and SpaceX manages to deliver on their promises of cheaper space launches, a return to the Moon and a mission to Mars (or fail to, for that matter) will we be able to say for sure which rocket was the true champion of human space exploration! But in the meantime, I’m sure there’s plenty of smack talk to be had by fans of both! Preferably in a format that rhymes!
And a tip of the hat to ERB!
ESA Prepares Revolutionary Air Breathing Rocket Engine

If new rocket engines being developed by the European Space Agency (ESA) are successful, they could revolutionize rocket technology and change the way we get to space. The engine, called the Synergistic Air-Breathing Rocket Engine (SABRE), is designed to use atmospheric air in the early flight stages, before switching to conventional rocket mode for the final ascent to space. If all goes well, this new air-breathing rocket could be ready for test firings in about four years.
Conventional rockets have to carry an on-board oxidizer such as liquid oxygen, which is combined with fuel in the rocket’s combustion chamber. This means rockets can require in excess of 250 tons of liquid oxygen in order to function. Once this oxygen is consumed in the first stages, these used up stages are discarded, creating massive waste and expense. (Companies like SpaceX and Blue Origin are developing re-usable rockets to help circumvent this problem, but they’re still conventional rockets.)
Conventional rockets carry their own oxygen because its temperature and pressure can be controlled. This guarantees the performance of the rocket, but requires complicated systems to do so. SABRE will eliminate the need for carrying most on-board oxygen, but this is not easy to do.
SABRE’s challenge is to compress the atmospheric oxygen to about 140 atmospheres before introducing it into the engine’s combustion chambers. But compressing the oxygen to that degree raises its temperature so much that it would melt the engines. The solution to that is to cool the air with a pre-cooling heat exchanger, to the point where it’s almost a liquid. At that point, a turbine based on standard jet engine technology can compress the air to the required operating temperature.
This means that while SABRE is in Earth’s atmosphere, it uses air to burn its hydrogen fuel, rather than liquid oxygen. This gives it an 8 x improvement in propellant consumption. Once SABRE has reached about 25 km in altitude, where the air is thinner, it switches modes and operates as a standard rocket. By the time it switches modes, it’s already about 20% of the way into Earth orbit.
Like a lot of engineering challenges, understanding what needs to be done is not the hard part. Actually developing these technologies is extremely difficult, even though many people just assume engineers will be successful. The key for Reaction Engines Ltd, the company developing SABRE, is to develop the light weight heat exchangers at the heart of the engine.
Heat exchangers are common in industry, but these heat exchangers have to cool incoming air from 1000 Celsius to -150 Celsius in less than 1/100th of a second, and they have to do it while preventing frost from forming. They are extremely light, at about 100 times lighter than current technology, which will allow them to be used in aerospace for the first time. Some of the lightness factor of these new heat exchanges stems from the wall thickness of the tubing, which is less than 30 microns. That’s less than the thickness of a human hair.
Reaction Engines Limited says that these heat exchangers will have the same impact on aerospace propulsion systems that silicone chips had on computing.
A new funding agreement with the ESA will provide Reaction Engines with 10 million Euros for continued development of SABRE. This will add to the 50 million Pounds that the UK Space Agency has already contributed. That 50 million Pound investment was the result of a favorable viability review of SABRE that the ESA performed in 2010.
IN 2012, the pre-cooler and the heat exchangers were tested. After that came more R&D, including the development of altitude-compensating rocket nozzles, thrust chamber cooling, and air intakes.
Now that the feasibility of SABRE has been strengthened, Reaction Engines wants to build a ground demonstrator engine by 2020. If the continued development of SABRE goes well, and if testing by 2020 is successful, then these Air Breathing rocket engines will be in a position to truly revolutionize access to space.
In ESA’s words, “ESA are confident that a ground test of a sub-scale engine can be successfully performed to demonstrate the flight regime and cycle and will be a critical milestone in the development of this program and a major breakthrough in propulsion worldwide.”
Bring it on.